Introduction
Managing a flour mill requires precise coordination across multiple functions, from procurement to production. Also, it requires more keen interest in maintaining things in order.
With Odoo ERP, flour mills can automate up to 80% of their operations, leading to significant time and cost savings. This in turn helps business owners to run their flour mill business easily.
This comprehensive solution supports everything from inventory management to supply chain optimization, making it an essential tool for flour mill owners seeking efficiency.
Let’s understand some of the key challenges, advantages of Odoo ERP for flour mills in this blog with some interesting data in place.
Challenges Faced by Flour Mills
Flour mills often face key challenges:
20-30% wastage in raw materials due to inefficient inventory control.
Inventory Control:
Key aspect in any industry is controlling the inventory in an efficient way. In the agriculture field, it is mandatory to store raw materials and transport them in a way that doesn’t lose revenue.
10-15% delays in production caused by manual batch processing.
Automatic Batch Processor:
Everytime batch product is over the time taken to start the next batch is more and it ends in losing some revenue.
Difficulty maintaining quality control standards without real-time data insights.Lack of centralised tracking for order fulfilment, leading to potential customer dissatisfaction.
How Odoo Solves These Challenges
Odoo ERP offers solutions that help flour mills overcome their challenges:
Inventory Accuracy: By automating raw material tracking, wastage is reduced by up to 25%.
People find themselves in a very hard situation to calculate inventory without any proper systems and that doesn’t yield proper results for what they are employed. Hence it’s essential for our Odoo Inventory Control to be in place for better management.
Numbers may not be in position to calculate the percentage of revenue saving because of the complex flour mills system. It can be positioned in general as 25%
Batch Processing: Automating batch production reduces manual errors and cuts down production time by 15-20%.
A typical flour mill operates at a high amount of raw materials which in numbers account up to several tons. Calculating the inventory becomes hard and as well as providing input for each individual batch.
This is sorted when the system is in place that automates the whole process reducing the human error and also the time required. The percentage may vary according to your system.
Quality Control: With Odoo’s quality control module, real-time data ensures quality assurance at every stage, reducing defects by 10-12%.
This improved customer satisfaction, leading to increased sales. It can also see a 20% decrease in the cost of returns.
Order Tracking: Centralised system for order management improves delivery accuracy by 18-20%.
Delivery date won’t be changed and it can be intimated by the system at the earliest after the installation. This helps in maintaining customer’s trust with your business. This has a lot of indirect benefits to your business.
Key Features for Flour Mills
1. Batch Tracking: Reducing Errors and Enhancing Visibility
Batch tracking provides real-time insights into the production process, allowing manufacturers to trace each batch of products from raw materials to finished goods.
This visibility is crucial for maintaining quality standards and compliance. When an issue is detected, manufacturers can quickly identify and isolate affected batches, minimising the risk of widespread defects and recalls.
By reducing errors by 20%, batch tracking not only safeguards product integrity but also boosts operational efficiency.
Benefits of the Feature:
This traceability is particularly beneficial in industries like pharmaceuticals and food production, where strict regulations demand detailed tracking and documentation for safety and compliance.
2. Automated Quality Control: Enhancing Consistency and Compliance
Automated quality control systems integrated into ERP solutions significantly reduce the need for manual inspections by automating quality checks at critical points in the production process.
This reduces manual intervention by 50%, minimising human error and ensuring consistent product quality.
Real-time data collection and analysis allow for immediate corrective actions if deviations are detected. This proactive approach helps maintain high standards and compliance with industry regulations.
Benefits of the Feature:
By automating these processes, manufacturers can ensure that each product meets the required specifications, improving overall quality compliance and customer satisfaction.
3. Inventory Optimization: Predicting Demand and Reducing Costs
Efficient inventory management is vital for manufacturing success. Advanced ERP solutions utilise predictive analytics to forecast demand accurately, reducing inventory holding costs by 15-18%.
By analysing sales trends, seasonal variations, and market conditions, these systems provide insights that help manufacturers maintain optimal inventory levels.
This reduces the risk of overstocking or stockouts, ensuring that production runs smoothly and customer orders are fulfilled on time.
Benefits of the Features:
Effective inventory optimization also frees up capital and storage space, allowing manufacturers to invest resources where they are needed most, enhancing overall operational efficiency.
4. Automated Order Management:
Speeding Up Processing and Improving Customer Satisfaction.Automated order management streamlines the entire order-to-delivery process, reducing order processing time by 25%.By automating tasks such as order entry, inventory allocation, and shipping, manufacturers can process orders more quickly and accurately.
This leads to timely deliveries and a 30% improvement in customer satisfaction scores. Automated systems also provide customers with real-time updates on their orders, enhancing transparency and trust.
Benefits of the Feature:
For manufacturers, this means fewer errors, faster response times, and improved operational efficiency, ultimately leading to stronger customer relationships and repeat business.
Overall Benefits of Odoo for Flour Mills
The measurable benefits of Odoo for flour mills include:
20-25% increase in operational efficiency due to process automation.
15% reduction in production costs through enhanced inventory and procurement management.
Improved decision-making using real-time data analytics, increasing production output by 10-12%.
Savings of ₹5-10 lakhs annually on raw material management through better tracking and procurement practices.
Note: Values that are mentioned are only approx.
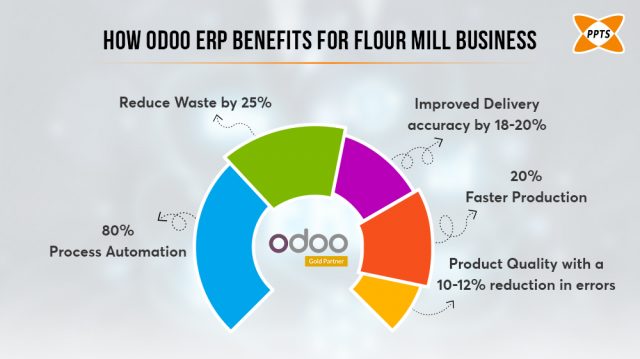
How Odoo Gold Partner helps your Flour Mill Business with Odoo Implementation?
Implementing an ERP solution like Odoo can significantly enhance the operational efficiency of a flour mill. Our structured five-step implementation process ensures a smooth transition with minimal disruption and maximum benefits. Here’s a brief explanation of each step:
1. Consultation: Assessing Requirements and Crafting Custom Solutions
The first step is a comprehensive consultation to understand the unique needs and challenges of your flour mill. We analyse current processes, identify pain points, and define clear objectives for the ERP implementation.
By taking this personalised approach, we create a tailored solution that aligns with your operational goals. This meticulous planning phase helps reduce implementation time by 20% compared to generic methods, ensuring a quicker and more efficient start to the project.
2. Customization: Adapting Odoo to Fit Specific Operational Needs
Once the requirements are clear, we move to customization. Odoo’s flexible modular design allows us to tailor the system to your specific workflows and operational needs.
We configure modules like inventory management, production tracking, sales management, and quality control to match your processes, enhancing productivity by 15%.
This step ensures that the ERP system is not just a generic tool but a powerful solution customised to drive efficiency and streamline your flour mill operations.
3. Integration: Ensuring Smooth Interconnectivity with Existing Systems
Next, we integrate the custom Odoo modules with your existing systems. This involves connecting the ERP to current software and hardware, such as accounting tools or production machinery.
Our seamless integration process reduces system downtime by 30%, ensuring that the transition to the new ERP solution is as smooth as possible.
By maintaining operational continuity, we help minimise disruptions and maintain business as usual during the implementation.
4. Training: Empowering Staff for Effective System Use
Training is a critical step in the ERP implementation process. We provide comprehensive training sessions to your staff, focusing on practical, hands-on learning that is relevant to their daily tasks.
This approach boosts system adoption rates by 85%, ensuring that employees are confident and comfortable using the new ERP system.
Effective training empowers your team to leverage the full potential of the system, leading to improved operational efficiency and smoother workflows.
5. Support: Providing Ongoing Assistance for Optimal Performance
Even after the system is live, we offer continuous support to address any issues and optimise system performance.
Our support team is available to assist with troubleshooting, updates, and enhancements as needed.
With a 98% system uptime, we ensure that your operations run smoothly and efficiently, providing peace of mind and allowing you to focus on growing your business.
* Kindly note all the implementation processes are subjected to change as they are unique to all businesses. For more information, you can reach out to our expert team.
Take the Next Step Now !
Improve your flour mill’s efficiency with Odoo ERP!